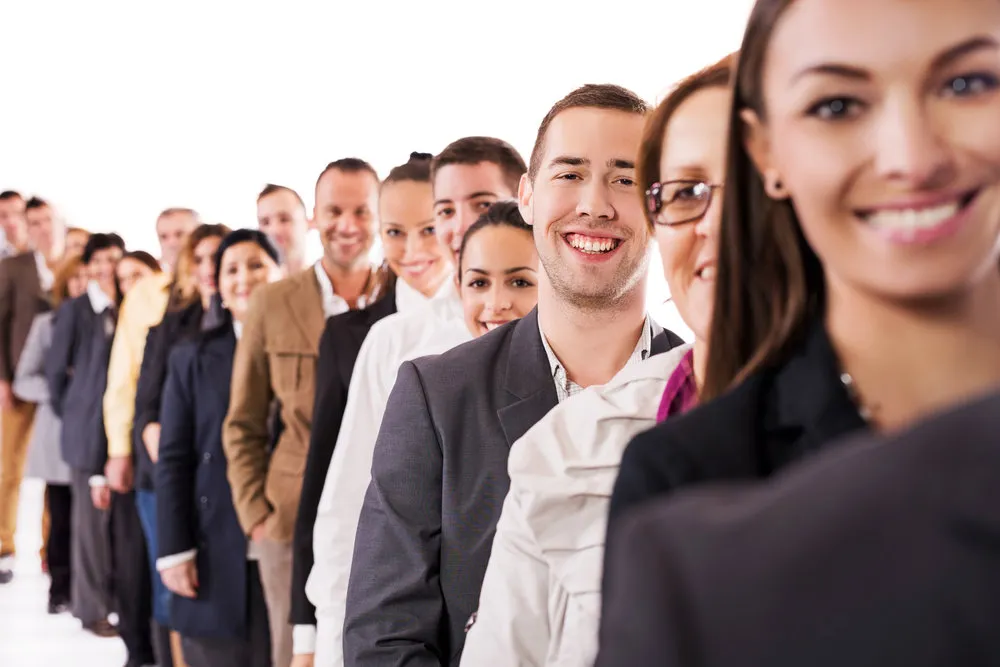
Automation is a loaded word in the American business world nowadays. Robots, drones, software, and artificial intelligence have moved off the pages of science-fiction into our warehouses, manufacturing plants, and retail floor spaces—but while they usher in a time of exciting growth, efficiency, and progress, they also portend a future where humans don’t have much to do.
That’s a scary concept for the millions of people who make a living doing jobs that robots will do one day, in the not-so-distant future. It’s also scary for the business leaders who have to weigh the advantages of a robot workforce—less costly, more efficient, never sick, etc.—with the real, present needs of their current human workforce.
There is no getting around it: One day,
robots will perform a lot of the tasks that humans used to. They’re doing it already: making boxes, moving inventory, measuring and cutting and transporting.
But they’re also not doing it: Robots are still typically incapable of doing things that require finesse, or operating in a space that is constantly changing. They lack the innate, unique human qualities that make us so useful: empathy, understanding, leadership, and the ability to pick the petals off a flower (and other tactile tasks) with ease.
So when it comes to the somewhat-dystopian concept of a future without work (on one hand, not having to work sounds nice; on the other, what will we do with ourselves?), we can say this: It may come one day. But not yet. And in the meantime, businesses should be investing in their human workforce, as well as in the tools that workforce uses to become even more efficient and effective, such as barcode scanners, mobile computers, and cloud-connected devices.
Robots aren’t ready to take over yet
It’s true that robots, drones, and other automated devices are a part of the workforce now. But to many companies,
they’re still more like “co-bots”—assisting humans by conducting continuous inventory, or scanning and taking stock of inventory and assets that are in hard-to-reach places.

But even a commerce behemoth like Amazon, which has asserted its place among all-time great companies by investing in greater efficiency and cornering the market on emerging technologies, is seeing issues with giving robots too much responsibility. That’s why people are still a major part of Amazon’s workforce. In fact, Amazon is helping pioneer a major mobile workforce of “work campers:" people who live in mobile homes and can travel from location to location to work warehouses, depending on the season and need.
According to an article in Wired, Amazon’s CamperForce consists of thousands of mostly retirement-age folks living nomadic lifestyles. CamperForce workers are hired as pickers, stowers, water spiders, and other positions that you might reasonably expect robots to have already taken over.
It’s not that Amazon doesn’t have robots—they bought out Kiva Systems, makers of warehouse-servicing bots, a few years ago, and utilize tens of thousands of them. But according to the Wired article, issues with the bots still abound:
They scooted around inside a dim fenced-in area—after all, robots don’t need light to see—on a floor nicknamed the Kiva field. Their job: ferrying open-faced shelving columns full of merchandise to stations operated by humans like me along the perimeter...
...They were supposedly the harbingers of a jobless dystopia in which manual labor would be obsolete. The reality was more slapstick. Our trainers regaled us with tales of unruly robots. They told us how one robot had tried to drag a worker’s stepladder away. Occasionally, I was told, two Kivas—each carrying a tower of merchandise—collided like drunken European soccer fans bumping chests. And in April of that year, the Haslet fire department responded to an accident at the warehouse involving a can of “bear repellent” (basically industrial-grade pepper spray).
It’s likely, if not guaranteed, that these robots will eventually do their jobs without spraying people with bear repellent or bumping into each other. But there’s a reason that even a company like
Amazon plans to hire over 120,000 people in 33 states to help when the holiday rush hits later this year: They know that, for now, nothing can beat the human touch.
Issues with change management
One of the reasons we can’t ignore the value of robots in the workforce is, quite literally, their value: After the initial investment you can have something like dozens of for every human you would employ.
But making that switch isn’t so simple, and many organizations aren’t equipped to deal with the fallout that comes with replacing their human employees.
For example,
according to The New Yorker, Danish hospital systems recently tried replacing their human orderlies with robots, which worked without complaint through all hours of the night at a much lower cost. But management wasn’t prepared for the reactions of the hospital staff, which included leaving “fecal matter and urine” in the charging stations.
That’s an unsettling (and gross) reaction, but not an entirely unexpected one.
Companies that move too quickly to replace their employees without providing those employees with alternatives, next steps, or further training will find themselves suffering the consequences. If the employees themselves don’t strike back, companies could see backlash in the form of public relations nightmares and community outrage. “Change management” is needed, and that comes with its own set of costs, in terms of both time and money.
Instead, bolster your existing workforce
Any good company with an eye towards the future will recognize the role that robots can and will play. But in the meantime, they can strike a happy medium by investing in their existing workforce, and giving their employees the tools they need to be more efficient without sacrificing safety, happiness, or profitability.
There have been lots of advancements in inventory and asset management thanks to barcode technology, which is utilized by Amazon, Target, Wal-Mart, and small businesses everywhere—even Etsy businesses.
Inventory and and asset management powered by barcodes are to businesses what analytics are to baseball: Getting in-depth numbers and statistics behind actions that were previously powered by gut instincts. Businesses can use these systems to see how efficiently their humans (and drones) are moving through the warehouses, when certain items can and should be re-ordered, when certain assets should be repaired or retired, and much more.
These management systems are just one part of
building a smarter warehouse, one where employees utilize the
Internet of Things—devices connected to the cloud, such as barcode scanners and tablet computers. Equipping employees with wearables like watches and glasses, or adding connectivity to industrial machinery so you can track their picking paths or their depreciation, are both excellent examples of this.
Technology shouldn’t be the downfall of humankind—it should be a force for good. If businesses, at least in the short term, put these technologies (IoT devices, analytics, etc.) in the hands of their workers and show them how much easier life can be, that’s a win for everybody.
Whether or not robots create a shortage in purpose for millions of blue-collar workers is a serious and pressing question. But let’s not let that dilemma stand in the way of what can work right now. And what works now is a better trained, better equipped, and more connected human workforce. Any company that misses that, is missing out.