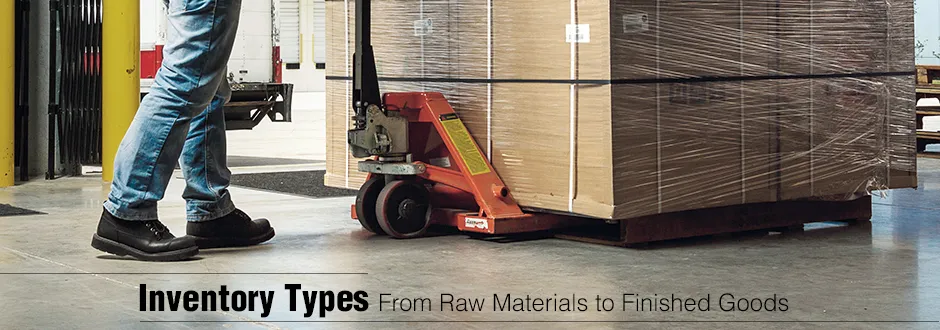
An understanding of the various inventory phases is crucial to managing production costs and earning profits. Inventory is classified as falling within three general categories: raw materials, work in progress, and finished goods.
Raw Materials
Raw materials are the primary components a business uses to make products. In the most primary stage, raw materials are extracted from minerals or produced from natural or chemically created substances. Those materials are then refined and used to make products for customers.
- Basic Categories: Raw materials separate into two basic categories: direct and indirect materials. Direct materials become a component of finished products. Conversely, indirect materials are used in the manufacturing process to produce finished products.
- Accurate Tracking: Accurate tracking of raw materials is crucial for successful warehouse management. This activity also ensures a smooth flow of business operations. When raw materials are received, they should be inspected to ensure the items match what’s been ordered from the vendor. The materials need to be logged within an inventory management system and labeled (typically with a barcode) for identification and storage.
- Appropriate Tracking Equals Efficiency: Appropriate tracking of raw materials keeps the product development processes efficient; improper tracking leads to poor order management. For example, inaccurate raw material counts lead to improper replacement ordering. This could result in work stoppage, which leads to missed deadlines and lost sales.
Work In Process Inventory
Materials currently be used in production are classified as “work in progress” inventory. Also called work in process, these items are no longer considered raw materials and also can’t be placed within the finished goods category. For this reason, companies focus on various strategies to reduce their work in process inventory.
- Lean Production Manufacturing: Lean production companies often try to eliminate work in process inventory because this phase ties up materials and prevents their use in other projects. To reduce large quantities of work in process inventory, pull only the materials you need for the current project.
- Quick Response Manufacturing: Quick response manufacturing (QRM) is another strategy companies use to reduce large amounts of work in process inventory. The ultimate goal of QRM is to reduce the time between when a customer places an order and the time delivery is made. To reach this goal, companies often use several small teams in the development phase. These teams concentrate on only a few tasks and are able to quickly complete projects. In this way, they keep work in process inventory at a minimum.
- Just-In-Time Manufacturing: Just-in-time inventory (JIT) is another development process aimed at reducing work in progress inventory. In a JIT environment, companies pull raw materials and complete products only when customers place orders. The JIT process reduces raw materials and work-in-process levels because inventory is pulled through the supply chain only when required.
Finished Goods
Finished goods are products ready for customers to purchase. When items reach this stage, it is in a company’s best interest to sell as quickly as possible to generate revenue, profit, and reduce costs associated with carrying too much inventory.
- Earn Revenues: Earning revenues represents a company’s cash inflow. However, the cost to make products must be taken into consideration. On accounting reports, this is known as cost of goods sold. It includes the amount paid for the raw materials, as well as the cost of labour to make products.
- Make Profits: If the cost of goods sold is subtracted from revenue, the result is gross profit. Making a profit is the main objective for most companies. To ensure profits aren't eaten up by storing too much stock, an automated inventory management system will track items from initial receiving to movement through production, and, finally, to completed sale.