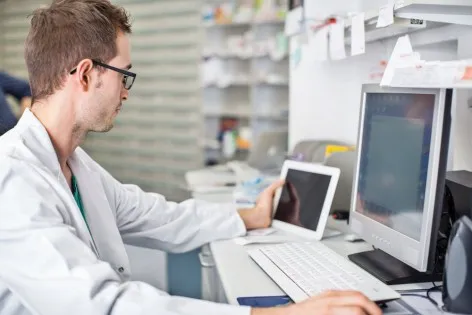
Barcodes are often associated with the cash register and buying basic products. Though with the rise of new barcodes, like the ubiquitous 2D barcodes, increasingly consumers are learning there is
more to the barcode than just prices. Barcodes can contain an enormous amount of information and have incredible potential to help with a variety of business needs. From checkout to check-in,
inventory needs to be tracked carefully, and barcodes provide an easy, efficient way to do so.
Health and medical care has proven to be one area where barcodes can save money, time, and lives.
In the UK, barcode implementation has led to some impressive success stories. From making sure patients get the right medication to keeping surgical theatres organized and efficient, barcodes are changing the way and the quality of health care in the UK.
Here are two recent examples of
UK barcode and health success stories:
Story 1: Stryker Medical Supplies Uses Barcodes For Compliance And Customer Satisfaction
For medical suppliers, like Stryker, the adoption of the US FDA’s Unique Device Identification (UDI) Final Rule and the NHS eProcurement Strategy, meant the company, along with other all medical suppliers, had to update their product labelling to comply with the new regulations.
While some companies might view the new regulatory compliance requirements as a burden, Stryker chose to use it as an opportunity to standardise their product identifiers and barcodes.
Stryker recognized that using standardised barcode protocols, like the GS1, on all their 72,000+ products around the world would make life easier for their customers and improve efficiency in the healthcare supply chain.
After analyzing their needs, Stryker decided that the global GS1-128 linear or Gs1 DataMatrix barcodes would be the most practical way to organize product data with a single, simple
barcode scan. To implement this transition, the company had to coordinate efforts among hundreds of people, across multiple product and selling divisions.
As explained by the GS1, this step involved bringing together data and information from:
- Regulatory (GMDN, authorized representative)
- Marketing (brand)
- Product development (dimensions, storage conditions)
- Supply chain (packaging level, unit of measure)
Once this information was brought together, Stryker began shipping their first GS1 labelled products in 2014 and is currently in the final years of phasing the project in.

Since implementing the barcode based system, Stryker has seen many benefits, internally and externally with their customers, including:
- Reduction in medical errors caused by incorrect identification of products;
- Simplified integration of device usage information into computer data systems;
- Quicker identification of medical devices associated with adverse events and accidents;
- More efficient reporting of problems and resolution of device recalls;
- Creating an easily accessible source of definitive identification information;
- Easier detection of counterfeit devices;
- Improved inventory management and supply chain efficiencies;
- Faster development of electronic patient records;
- Helping identify similar or replacement devices when needed in a shortage.
By now, more than 28,00 of Stryker devices meet the new standard, and the remaining should be up to date by September 2018. The new barcodes allow Stryker to fulfill critical compliance requirements and make it easier for hospitals to use Stryker devices and increase efficiency and patient safety. A barcode success story by any standards.
Story 2: Great Ormond Street Hospital Solves Stock Problems With Barcodes
One of the biggest challenge for any hospital is the need to monitor the daily use of high-cost consumables.
At the Great Ormond Street Hospital (GOSH), started in 1852 as the UK’s first pediatric hospital, they treat over 150,000 patients a year for some of the rarest and most complex conditions. As a national centre of excellence and an NHS Trust, cost saving, increased productivity and efficiency, and most importantly improving patient care are top priorities.
The cardiac catheterisation laboratory at GOSH utilizes high-cost consumables on a daily basis, requiring greater focus on accountability and reducing costs. GOSH needed a way to computerize its stock in order to effectively monitor its usage as well as to ease the burden on staff and doctors so they could focus more on patient care and safety.
Keeping track of this kind of stock is important to effectively run the hospital. The hospital needed the system to:
- Ensure stock levels are maintained;
- Reduce wastage of expired stock;
- Reduce expenses by ordering only the stock needed;
- Accurately cost procedures for patients based on what consumables are used
GOSH decided to use the
Wasp Barcode Inventory Control solution to label the consumable in its cardiac catheterisation laboratory. To do so, the hospital first categorized the catheterisation lab’s stock into logical, manageable sections, a consistent nomenclature for item descriptions was developed. The items were then entered into the Wasp database, and barcodes generated for each individual stock item. Rather than placing a barcode label on each stock item, the hospital elected to create a folder containing the barcodes of the stock items.
With the system in place, managing the lab’s stock became easy, efficient, and intuitive, as did generating accurate procedure cost reports. When cath lab stock arrives, it is scanned into stock. A mobile device allows staff to scan the inventory out of stock when it is used on a patient, it also allows the staff to identify and itemize what stock is used on which patient.
The automated
barcode scanning system eliminated human data entry error, greatly increases the speed and efficiency of linking stock used to a specific procedure and patient, and instantly updates the information in a central database that can be used when creating itemized patient cost reports or to keep track of stock levels and reordering.
By having a barcode based system in place, GOSH is able to:
- Quickly and accurately determine cost per procedure;
- Easily create professional looking reports that include a list of items used and total cost for procedure;
- Keep track of total cost of cosumables used per month and per year, average cost of certain procedures, and total value of items in stock, with the click of a button;
- Ensure needed consumables are always in stock;
- Automate stock usage to reduce wastage;
- Simplify end-of-year stock audits and create discrepancy reports.
As a lab representative explains, “The Wasp system is flexible and provides a good value for our money. It is an efficient stock control solution in a clinical environment.”
The new system makes it easier and more efficient for lab workers to do their job, ensures patients get the right treatment with the right equipment, and allows the hospital to accurately track procedure costs. This means that doctors and staff can spend more time focusing on patients and healthcare.
Barcode based systems would seem to be a no-brainer for hospitals. They increase efficiency and savings while also improving patient care and safety. Are you making sure to use barcodes at your hospital?